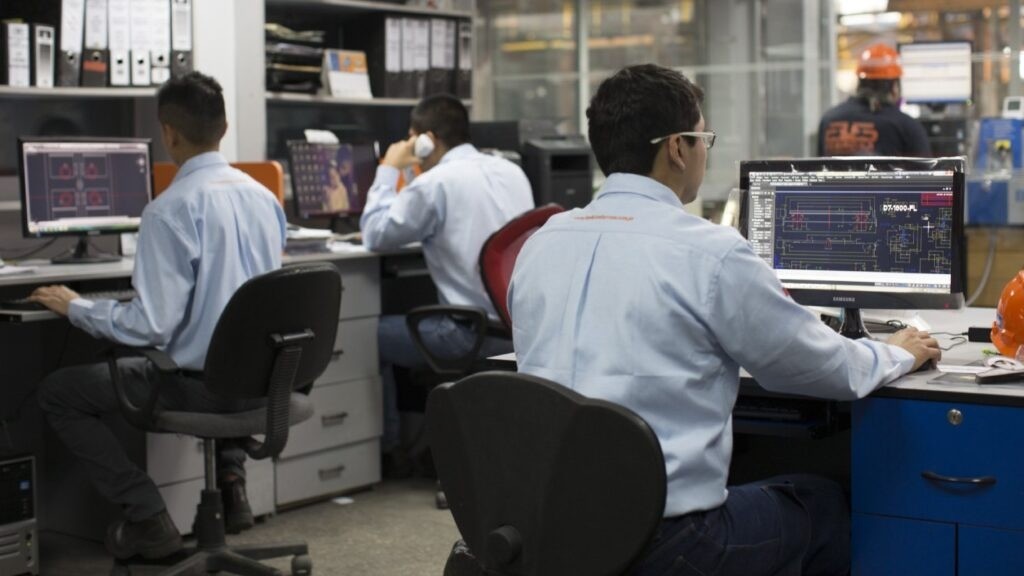
We develop and design the pieces from the taking of measurements of a physical sample or drawings of the client. ROCKY y ANSYSfor this purpose, we have qualified personnel who can be transferred to the plant operation to carry out the work “in situ” and with digital measurement tools, scanners and calibrated profiles according to the standards requested by our ISO 9001-2015 accreditation, managing to translate into 3D measurements and simulations using software such as Inventor, SolidWorks, ANSYS and ROCKY.
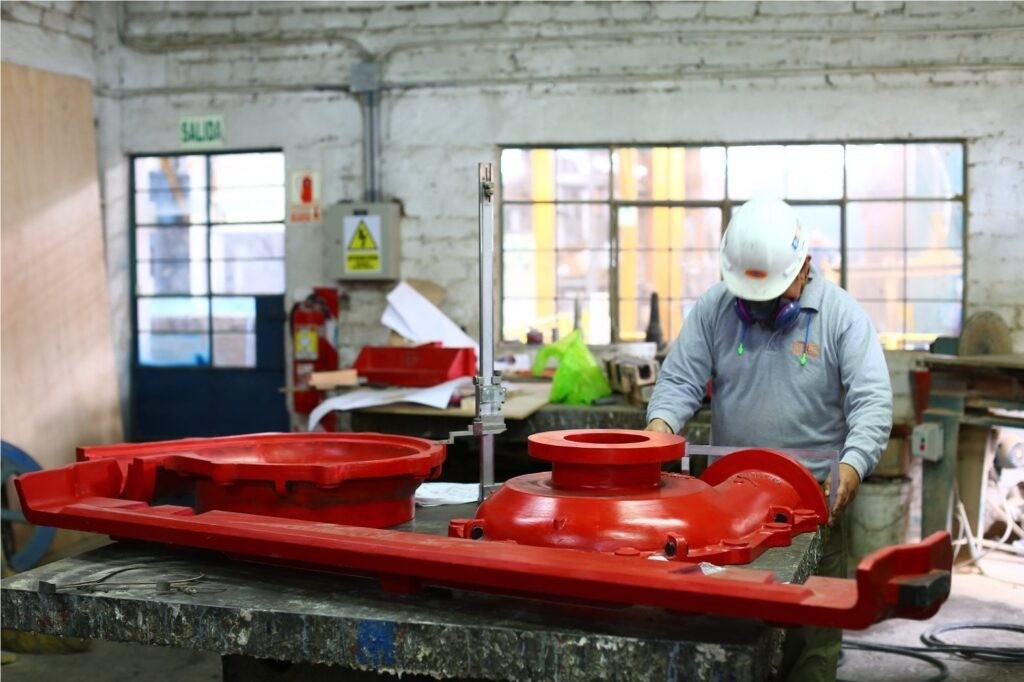
Wear Parts Modeling for the Mining and Cement Industry. We have a complete model shop to manufacture different designs of models and adobonera plates for mass production, in different materials: wood, resin and metal (aluminum).
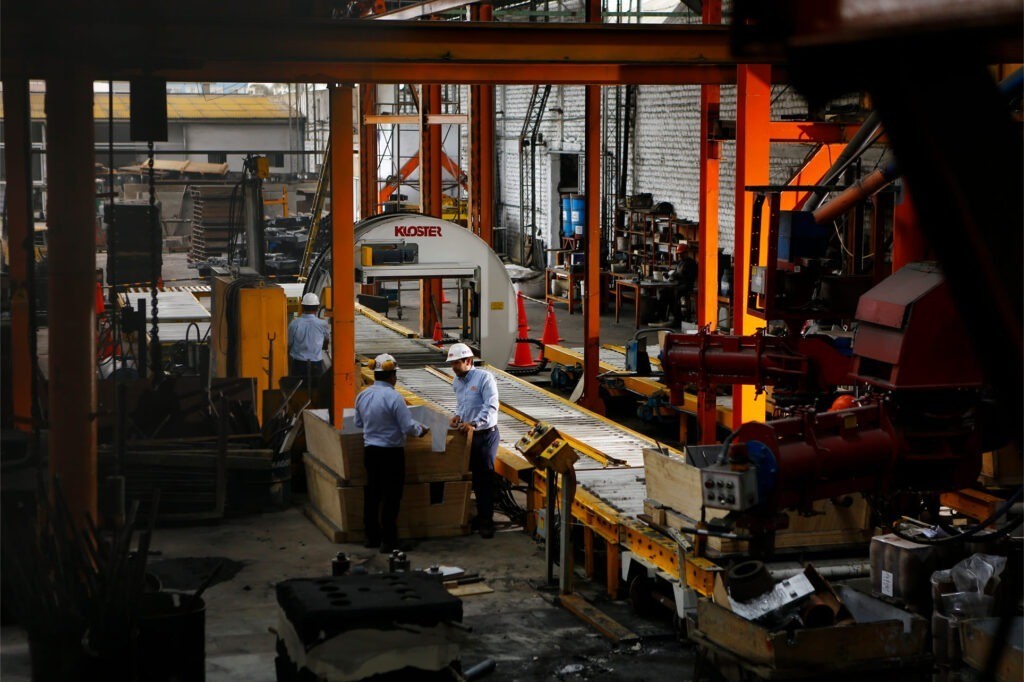
We have an Automated Molding line (Fast Loop System) (Fast Loop System) of 10 molds per hour for series production. We use ecological supplies, taking care of the environment and our collaborators. We recover 100% of the sand used in the production process.
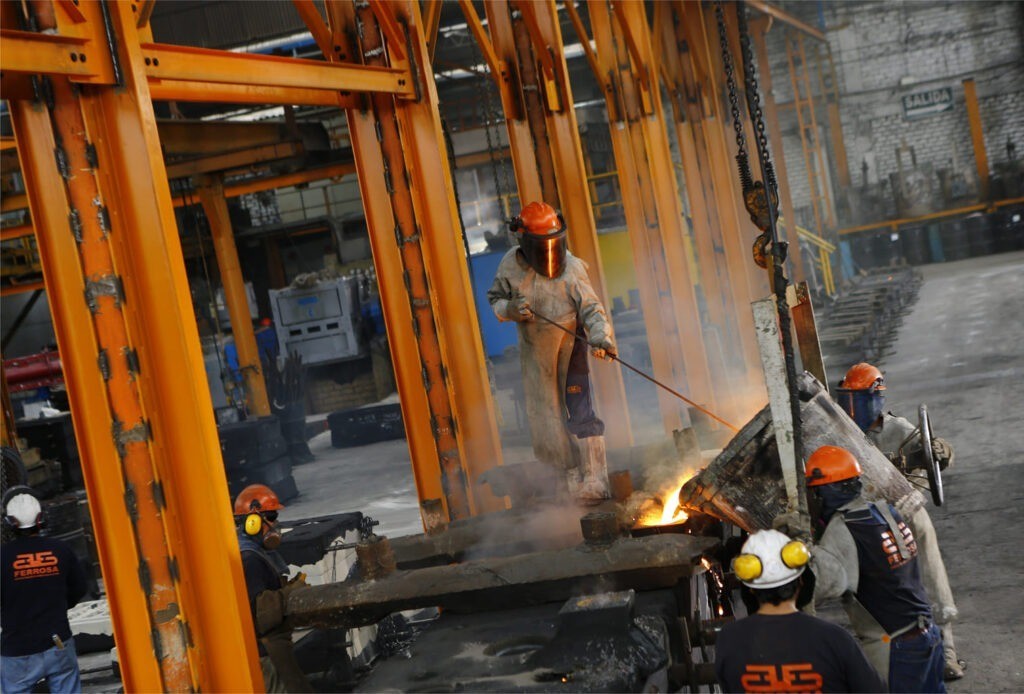
Casting of wear parts for the Mining and Cement Industry. We manufacture cast parts from 20 kilos to 2000 kilos. We work in induction furnaces for fusion of 300 kilos, 600 kilos, 1500 and 3000 kilos, which allows us to have great casting flexibility for parts of different sizes. We have various overhead cranes of 3 and 5 tons for the hauling of parts and molds.
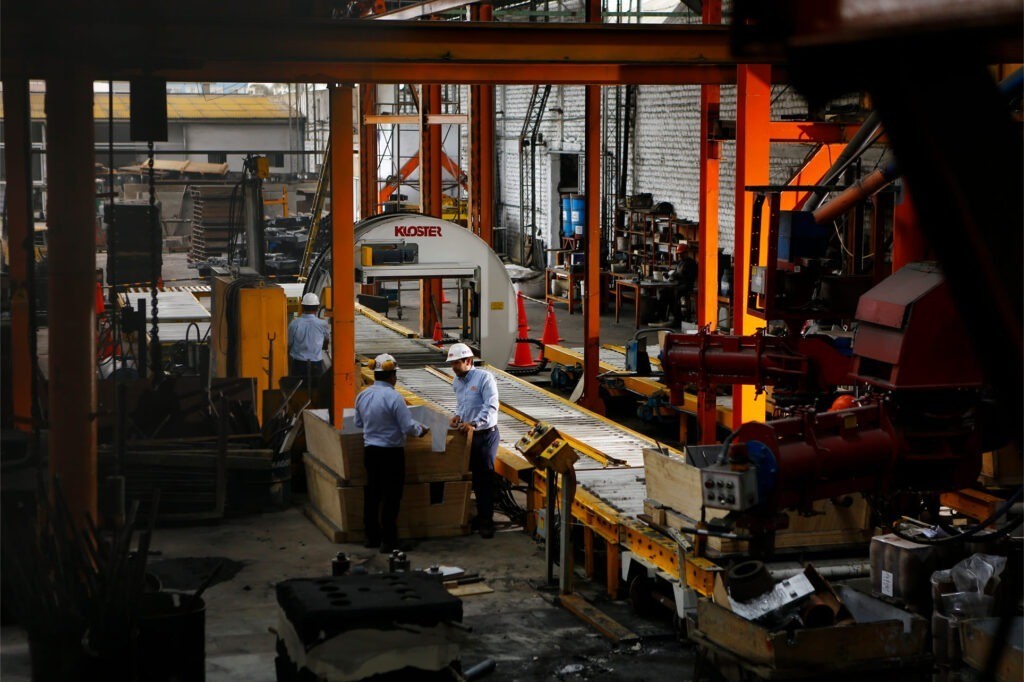
Wear parts finishes for the Mining and Construction industry. We use shot blasting systems, various grinders (pendulum, pedestal and portable) and a booth to paint the parts if the client so requires. We have strategic alliances with Metalworking for the machining of parts. They have various Hass Machining Centers with a 20-tool station, Hass CNC lathes and other conventional lathes with overturning of more than 1000 mm. In addition to this they use planes, drills and a variety of tools to deliver fully machined castings.
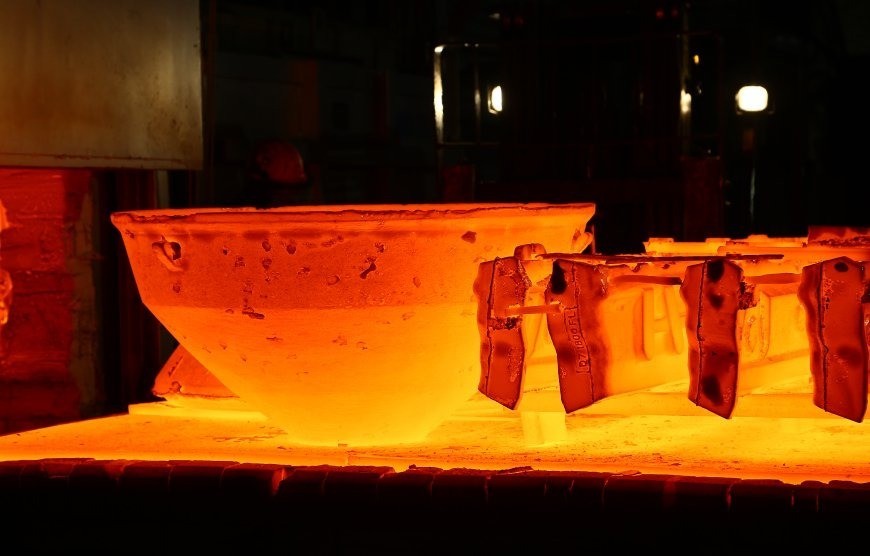
Casting of wear parts for the Mining and Cement Industry. We have three PLC-controlled electric furnaces that execute the most complex heat treatment curves for high-alloy steels, automatically transferring them to the computer, as well as alerting process control engineers through lights and alarms. We have a 60 cubic meter water quenching and hyper quenching pond with a steam dispersion system and a cooling tower to keep the water temperature below ambient temperature, and two powerful fan systems for forced air quenching.
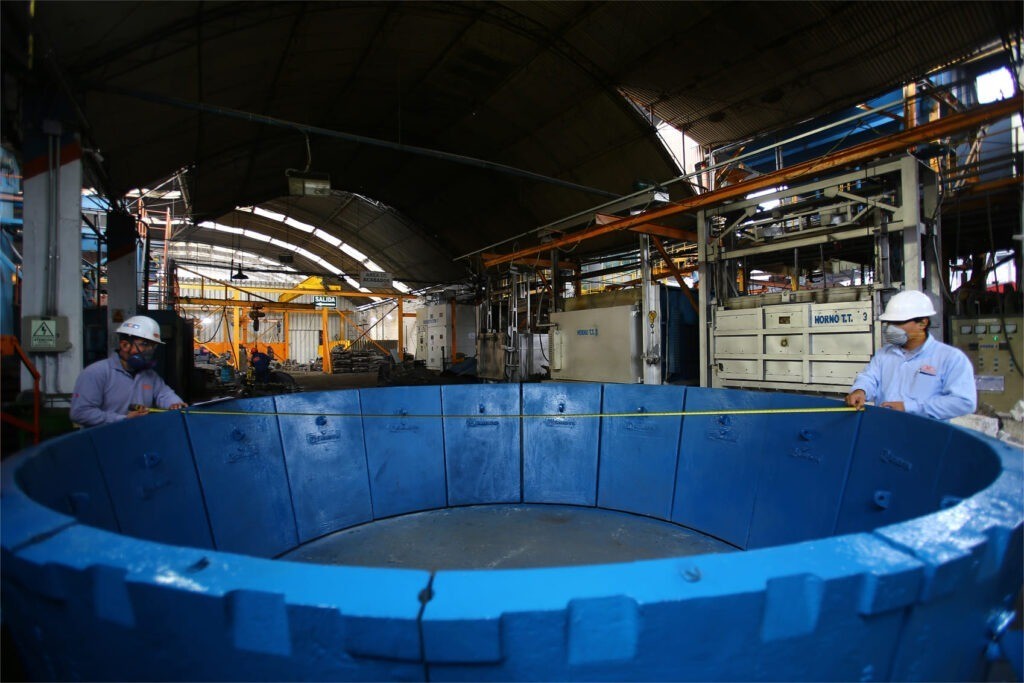
Mediante la certificación ISO 9001:2015 Quality Control and Laboratory Lima. Casting of wear parts for the Mining and Cement Industry. We exercise strict control over raw materials such as silica sand, resin and scrap. We verify by international casting standards, the dimensional tolerances of the produced parts. We permanently carry out LOI, ADV, Acid Demand, Granulometry, Microscopy, Humidity, Permeability tests, among others, on sand and sand-resin molds. The furnace load calculation is corroborated with the Optical Emission Spectrometer and the temperature of the metal is measured through an immersion pyrometer before being poured into the molds. To control cast parts, we carry out non-destructive and destructive tests. For the former we have penetrating dyes, magnetic particles, hardness, dimensional inspection and spectrometry analysis. For the latter, tensile and impact tests and a complete metallography laboratory with microphotography included.